Purchasing & inventory support agent at HUBTEK (2022-2023)
Hubtek is based on Miami and has employees also in Colombia, Mexico and Ecuador.
I was assigned with to a customer account that is also based in Miami and has operations in the Caribbean.
In this job position I was hired for the purchasing and inventory department.
I began analyzing stock availability to understand replenishment needs at the warehouse.
Some products are slow movers while others have a higher rotation.
Other products have expiration dates and have to be dispatched fast enough.
Myobjective is to make this process better.
The projects assigned to me were:
a) Understanding the procurement modules in the inventory software (INFOR ERP).
b) Updating product item codes.
Nominated employee for INNOVATION
I was nominated for the firt time for the company awards.
It was for sharing new ideas for the operations.
Nominated employee for PASSION
I was nominated again in the companny for my proactivity.
a) Procurement modules management project
INFOR is an ERP targeted to manage inventory. It contains different modules that can identify inventory behavior. Then the inventory operator can correct the usage of it.
Some parameters considered in the logic of the system are:
- Lead time
- Usage
- Vendor rules
- The product items involved
-Product Line configuration
The objective of this project was to understand and offer guidance to my team on how use INFOR tools for this purpose.
The result will enhance the efficiency of the company, spending less time using excel spreadsheets for stock forecasting. That is automation.
INFOR will suggest purchase orders for the stock replenishment.
*To understand better the operational pain points I was shadowing purchasers in the process of forecasting inventory stock with manual excel spreadsheets. I did follow up to orders and noticed delay in the lead time of the stock.
From the sales team perspective that implied low fill ratios and suboptimal invoicing at the end of the month.
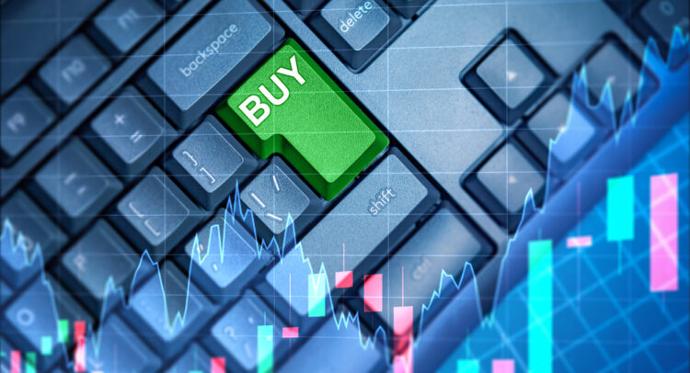
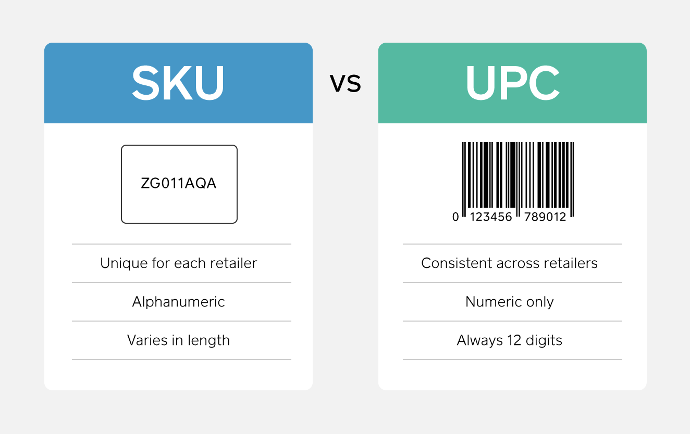
b) Product code projects
The pain point of this project is the delay in data entry. Many SKUs were different between the subcontracted warehouse and our company. Most importantly, the idea is to have the product code of the box in the system.
This change to the correct item number in excel is a process to make the inventory control and orders process less time consuming. This change was made to vanish misunderstandings between the warehouse workers (physically in the WH) and the system purchasers (working remotely).
*To understand better the operational pain points I was processing sales orders for some months. I was doing follow up to orders and noticed delay in the lead time of the stock.
Operational SOP for the company
A plus besides my project was building an SOP.
I created different step by step diagrams in Michosoft One Note for the operational departments of the company.
With this operational manual I did a map regarding main operations in:
-Sales department
-Purchasing department
Logistics deparment
This effort was targeting to reduce the training time for new employees.
The SOP was made with of daily tasks and mostly consisted in screenshots of the INFOR ERP Software.
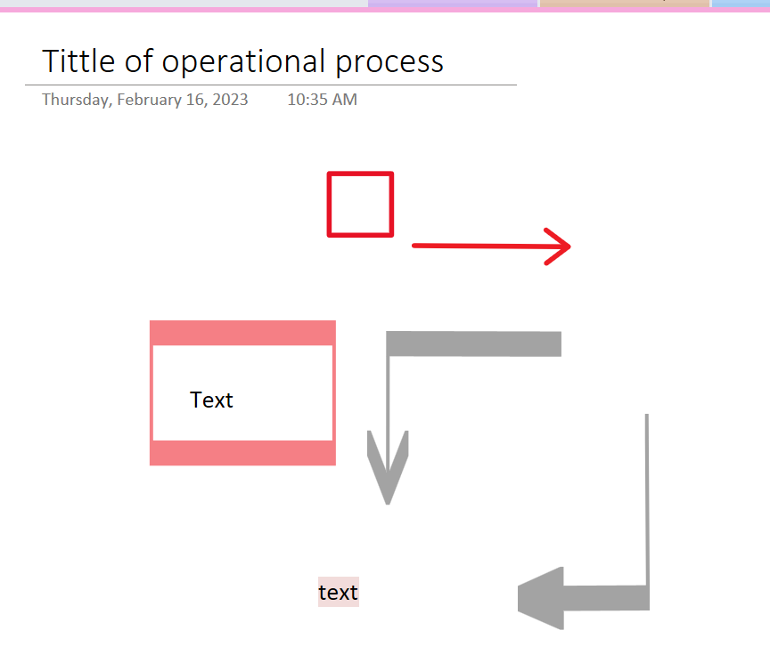
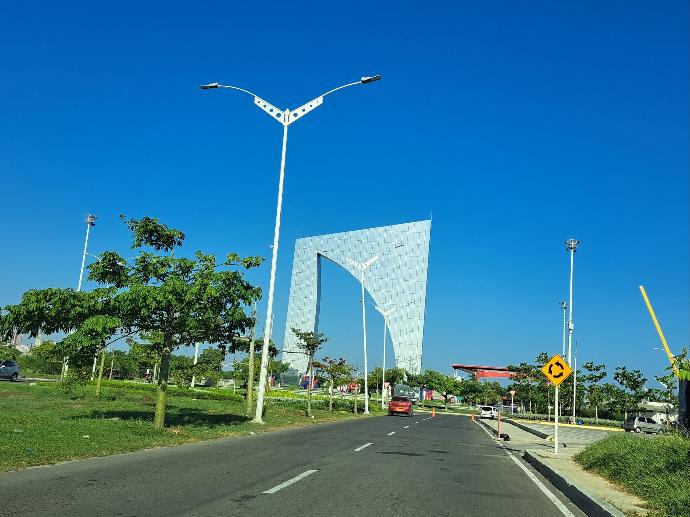
Visit to Barranquilla
Our account managers came to visit from Miami to Colombia in December 2022. As I work and live in Medellin I also traveled to this beautiful city.
This was an opportunity to know in person the purchasing and logistics team.
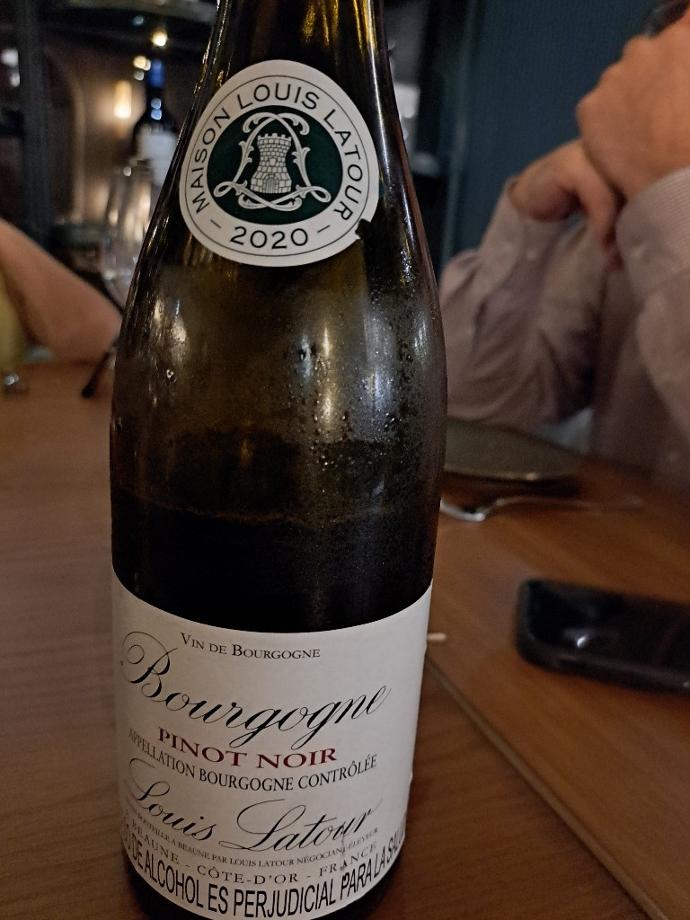
Dinner at the end of the year
At night it was also possible to share a dinner and discuss experiences during the year.
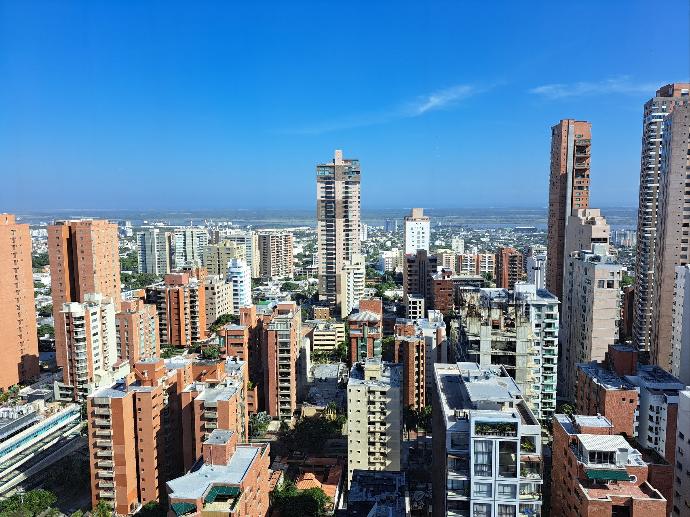
Discussed results
The customer account increased its reveneu in the Caribbean. We were more exposed about the sister companies in the Caribean and the operations in Miami.
Managers visit Medellin
The Operations Manager (from Miami) and the Purchasing Manager (from Trinidad & Tobago) visited the Colombian Team in Medellin.
We had the opportunity to take into practice the theory learned in a previous workshow on how to execute Replenishment system reports. In the link below you will notice additional details on the learning about inventory management.
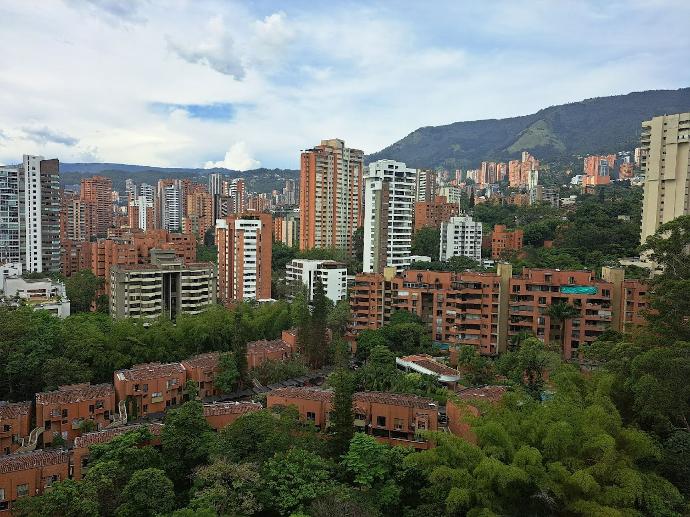